Manufacturing Method Development and In-House Production Technology
Somic Ishikawa has built an integrated production system that allows us to carry out nearly all processes within our facilities. We have in-house from design and development to production, and shipping to our customers. Our advanced R&D and product development departments are not only things that help us maintain our world-class manufacturing technologies, but the equipment built in-house makes a great contribution. These allow us to keep a high-quality level of products, and make timely improvements to them, which would not be possible if out- sourced. We also strive for the development of better production methods by focusing on central concepts like "automation," "simple & slim," and "machining reduction & non-machining." Never being content with where our level of quality is at and constant improvement upon it, help to keep Somic Ishikawa the top in manufacturing.
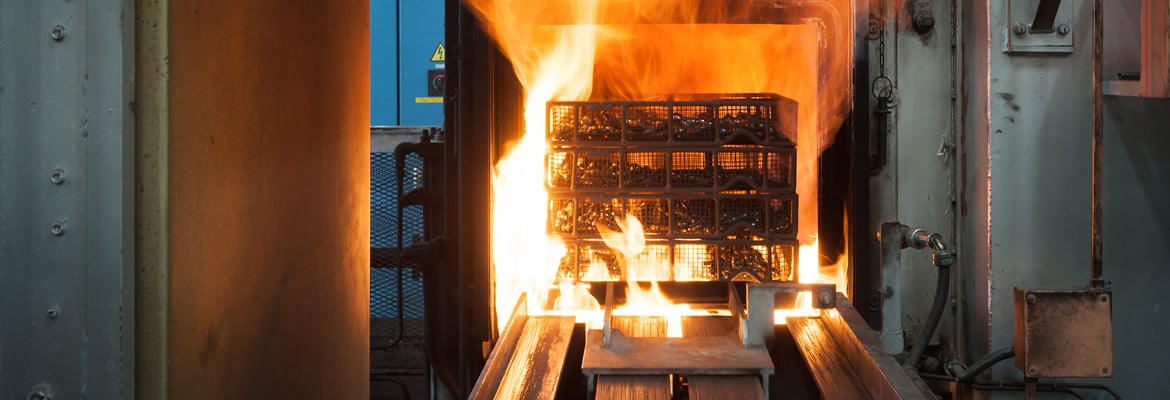
[Manufacturing Method Development]
Refining Integrated Production
Automation
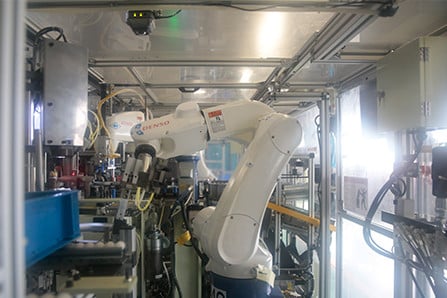
There is a reason why Somic Ishikawa's market share is at the top in Japan. We have introduced robots into every step of the production process for a stable output and delivery of products namely automation of production processes.
Components supply to the machines is one example of automation. In the old days, an operator would stand in front of a machine, push a switch, and load components into a machine. Nowadays, all we have to do is to put components into a box, carry it over to a machine, and then the machine will automatically judge the direction of the box and start the supply. When it comes to transferring parts between machines, unmanned carts called automatic carriers are used. Robots do the final packing work as well for the completion of the last process.
Automation such as this reduces the workforce from three operators to one thus contribution to production efficiency.
Simple & Slim
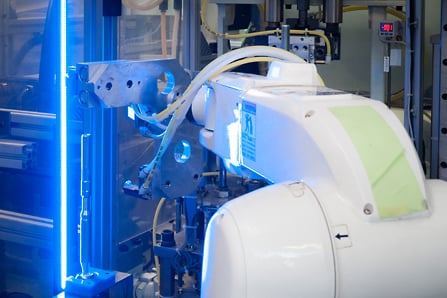
Further improvement of efficiency is essential to increase our market share in the global market. Somic Ishikawa develops and improves the manufacturing method based on basic concepts of, "Simple, Slim, Compact, Smart, and Speedy."
One example is shortened processes for the shorter delivery time. Cost reduction by reduced travel distance by operators is another. We apply this basic concept for the design of production equipment also. Our goal is to downsize everything by half, including machine size, capital investments, and lead time.
We have success in reducing a machine height from as a high as the ceiling down to eye level.
Reduced-Machining and No-Machining (Cold Forging Technology)
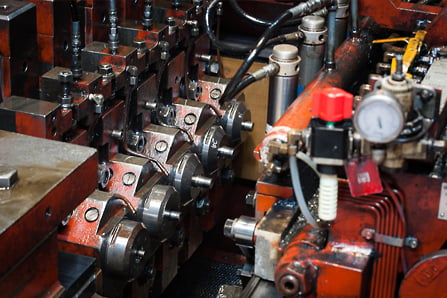
One superior production technology that benefits Somic Ishikawa is cold forging. Different from hot forging that forms metal by applying pressure at high temperatures, cold forging forming is ambient temperature and is known for high strength and accuracy.
Somic Ishikawa, as a pioneer, introduced this technology to Japan during the 1960s. This technology coupled with over a half a century of accumulated know-how has garnered us the trust of many car makers and allowed us to deal with all kinds of product variations.
To refine this technology further, minimalize machining labor cost as much as possible, cut costs, and improve efficiency, we have turned our focus onto reduced machining and no machining processes.
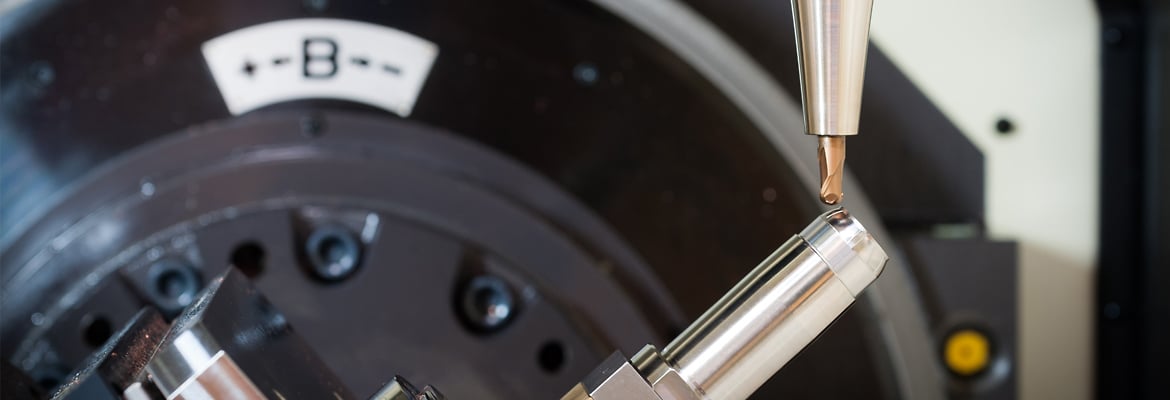
In-House Production Technology
Personifying 100 Years of Original Technologies
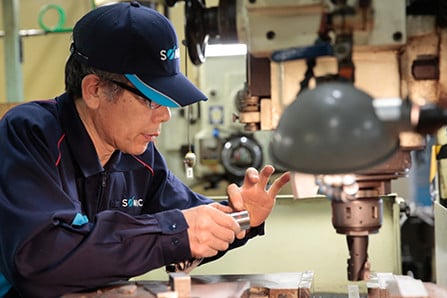
Somic Ishikawa has built up many original technologies since the company's establishment. Cutting-edge R&D and design are both needed to meet the requirements of the time. Machining and assembly equipment is used for the manufacture of designed parts. Somic Ishikawa builds most of the equipment, vital area in the industry, in-house.
Tooling and assembly equipment, which are critical to both the beginning and end of the manufacturing process, is produced 100% in-house. We are fully aware and responsible for the critical safety parts we manufacture that can never fail, not even in the worst-case scenario.
In addition to tooling and assembly equipment, machining measuring and testing equipment used for in-house valuations, are all designed and made in-house. Combined with our in-house production technologies, we not only maximize the utilization of our know-how but increase our products' quality and originality as well.